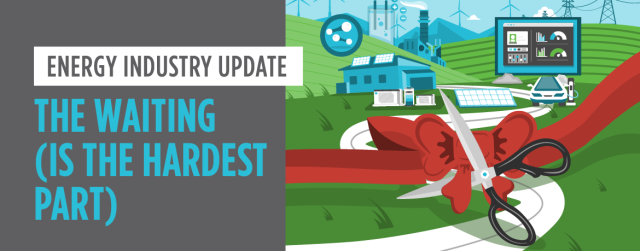
When dealing with system maintenance, many plant managers prefer to have a repair or replacement part in his or her warehouse, just in case. On the other side, some supply chain professionals argue for lower inventory levels to reduce financial holding costs.
Leveraging data from the Utility Material Management Benchmarking Consortium (UMMBC) 2015 Warehouse Survey, ScottMadden examined whether more on-site material actually improves material availability. And, if it does, by how much? This complimentary report is the first of a four-part series and takes a deep dive into our analysis, offering insight into best practices for improving material availability.
ScottMadden is a founding member of the UMMBC and has been conducting independent research studies on behalf of the consortium since 2007. ScottMadden has been assisting leading utilities with improving their supply chain operations for more than 20 years. Contact us to learn more about strategies for improving material availability and solutions to lower your stock-out rates.
Be sure to check out all of the articles in this series.
FULL ARTICLE
Anyone dealing with system maintenance has experienced a moment when a repair or replacement part was not on hand when needed. This can result in everything from a minor inconvenience to a costly outage extension. Given this experience, there is a tendency to think, “If we only had more material in our warehouse, we wouldn’t have these shortages.” Many plant managers would prefer a “spare plant” in his or her warehouse, just in case. On the other side, supply chain professionals argue for lower inventory levels to reduce financial holding costs. In this article, we examine whether more on-site material actually improves material availability. And, if it does, by how much?
This is one of several questions examined by ScottMadden using data compiled by the Utility Material Management Benchmarking Consortium (UMMBC)[1] in their 2015 warehouse survey. This survey collected detailed data from 286 warehouses operated by 15 leading utilities. The breakdown of warehouses by business unit is shown in Figure 1.
Figure 1: Warehouse Participants by Business Unit
Utility Business Unit |
Number of Warehouses |
Fossil Generation – Coal |
63 |
Fossil Generation – Gas |
41 |
Fossil Generation – CT |
26 |
Nuclear Generation* |
31 |
Hydro Generation* |
48 |
Distribution Only (Electric & Gas) |
34 |
Transmission and Distribution Combined (Electric & Gas) |
43 |
Total |
286 |
*not included in this analysis |
|
Stockout Rates
In the 2015 survey, participants were requested to provide average Stockout Rates for the prior year as a measure of material availability. The Stockout Rate was defined as the percentage of items not available upon the requested need date. As shown in Figure 2, the resulting data indicated that median Stockout Rates were relatively low across all business units ranging from a low of 0.1% in combined transmission and distribution (T&D) warehouses to a high of 5.0% in distribution-only warehouses.
Figure 2: Average Stockout Rates by Business Unit[2]
Business Unit |
Minimum |
Median |
Maximum |
N |
Fossil Generation – Coal |
0.1% |
2.4% |
16.0% |
29 |
Fossil Generation – Gas |
1.1% |
4.0% |
5.7% |
18 |
Fossil Generation – CT |
1.5% |
1.5% |
6.9% |
14 |
Distribution |
0.0% |
5.0% |
7.5% |
29 |
Transmission and Distribution Combined |
0.0% |
0.1% |
2.5% |
37 |
On-Site Material
The UMMBC survey also collected the dollar value of Total On-Site Material divided into three categories as shown in Figure 3.
Figure 3: Median On-Site Material by Category and Business Unit ($000 US)
Business Unit |
FERC 154 |
Consigned |
Capitalized |
Total On-Site Material |
Fossil Generation – Coal |
$12,079 |
$8 |
$3,369 |
$13,144 |
Fossil Generation – Gas |
$3,848 |
$0 |
$2,025 |
$4,947 |
Fossil Generation – CT |
$1,103 |
$0 |
$0 |
$1,103 |
Distribution |
$787 |
$0 |
$208 |
$1,140 |
Transmission and Distribution Combined |
$2,878 |
$70 |
$294 |
$4,641 |
Most of the On-Site Material was FERC 154 inventory. The next material category was Consigned Material, which was owned by third parties but held at the utility’s warehouse. Few warehouses in the database held Consigned Material. The third material category was Capitalized Material, material on-hand that has no dollar value in inventory insofar as it was expensed to projects upon acquisition. Neither Consigned Material nor Capitalized Material showed as “inventory” on the utility’s books, but they were stored in the warehouse and issued as needed. As such, they impacted the utility’s overall Stockout Rate. For this reason, they were included in our analysis.
On-Site Material versus the Stockout Rate
Armed with this data, ScottMadden developed a series of correlations and regression equations using the Stockout Rate as the dependent variable and On-Site Material as the independent variable. The results are shown in Figure 4 below.
Figure 4: Correlation and Regression Test Results for Stockout Rate versus On-Site Material
Measure |
Coal |
Gas |
CT |
Total GEN |
Dist |
T&D |
Total WIRE |
TOTAL |
Number of Cases |
29 |
18 |
7 |
51 |
28 |
18 |
46 |
97 |
Correlation |
-0.447 |
-0.385 |
-0.588 |
-0.426 |
-0.15 |
0.052 |
-0.144 |
-0.24 |
R Square |
0.199 |
0.149 |
0.346 |
0.181 |
0.023 |
0.003 |
0.021 |
0.058 |
Y-Axis Intercept |
0.07 |
0.084 |
0.223 |
0.089 |
0.084 |
0.041 |
0.069 |
0.073 |
Reg. Coeff. *10,000,000 |
-0.014 |
-0.039 |
-0.379 |
-0.022 |
-0.01 |
0.001 |
-0.004 |
-0.008 |
As the previously mentioned plant manager suspected, warehouses with more On-Site Material actually do have lower Stockout Rates. This relationship holds true for all types of generation warehouses and for distribution warehouses as well. However, the opposite occurs in T&D warehouses where more inventory is associated with higher Stockout Rates.
Before starting to increase On-Site Material to improve material availability, a bit of caution is in order. The regression analysis showed that the strength of the above relationships was very weak. Material levels “explained” from 0.3% (T&D warehouses) to 34.6% (gas generation warehouses) of warehouse Stockout Rates. Keeping in mind that warehouse Stockout Rates were very low to begin with, it took a great deal of additional material to significantly lower the Stockout Rate. In coal generation warehouses, for example, doubling the volume of On-Site Material would lower the Stockout Rate by less than one-hundredth of a percent. Not an encouraging trade-off.
So, while every company has a war story about the time when a $150 part caused a delay or problem costing thousands (or millions) of dollars, the data simply does not support increasing On-Site Material to improve material availability. Yes, the relationship we anticipated proved out, but it is far too weak to support growing inventory as a strategy for improving parts availability. Additionally, the analysis only scratches the surface on whether or not a particular utility’s inventory is the right inventory. Thus, materials managers will need to look to other solutions to lower Stockout Rates and improve overall inventory health such as better demand planning, more sophisticated item forecasting capabilities in the absence of better demand planning, and enhanced investment recovery mechanisms for the inventory that is “stranded” and no longer providing value.
ScottMadden’s long history of working with electric utilities and other asset-intensive companies and deep understanding of the key performance levers in supply chain gives us a clear lens through which to view efficiency and effectiveness. Additionally, ScottMadden’s proven methodology to uncover the true drivers of inventory levels and develop realistic improvement plans is the most comprehensive approach in the industry. We encourage you to learn more about our capabilities and opportunities to optimize your inventory levels.
To learn more about ScottMadden’s supply chain practice, please contact us.
About ScottMadden’s Energy Practice
We know energy from the ground up. Since 1983, we have been energy consultants. We have served more than 300 clients, including 20 of the top 20 energy utilities. We have performed more than 2,400 projects across every energy utility business unit and every function. We have helped our clients develop strategies, improve operations, reorganize companies, and implement initiatives. Our broad and deep energy utility expertise is not theoretical—it is experience based.
[2] Not all warehouses measured or were able to report average Stockout Rates. Nuclear and Hydro warehouses are excluded. “N” refers to the number of warehouse for which this data was submitted.
Sussex Economic Advisors is now part of ScottMadden. We invite you to learn more about our expanded firm. Please use the Contact Us form to request additional information.