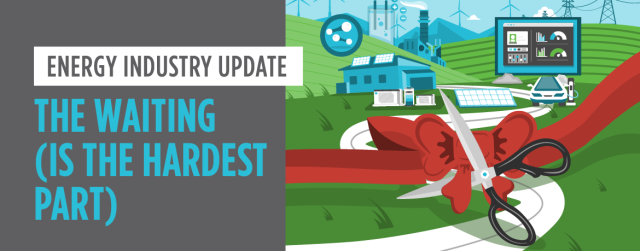
Who could have guessed on January 1, 2020, what the remainder of the year would hold? Personal protective equipment (PPE) is now critical for most operations, and risk management and transparency within the supply chain is more important than ever. We are learning how to be productive while working from home (WFH) and creating new safety and social distancing practices for people who must come to work.
As we move forward, we must respond to changing business priorities as the effects of the pandemic reverberate through supply chains. During the initial response, we altered work priorities, deferred maintenance, and changed many long-term plans to ensure we could address immediate needs. We also learned firsthand the importance of traditional responsibilities of the supply chain function like providing adequate inventory levels, managing supplier risk, developing local supply, and tightly integrating with the plans of our businesses. These changes and lessons will continue to have an impact as we get back to work in the “next normal.”
Drivers of Change
Understanding how the pandemic has fundamentally changed supply chains starts with understanding what is driving the change. As shown below, there are four major drivers that require updates to our supply chain strategies.
ScottMadden Supply Chain Reference Model
Reviewing these drivers of change against ScottMadden’s Supply Chain Reference Model is a useful exercise to ensure leaders are thorough in their consideration of the impacts of the pandemic.
The model includes six functions at the center:
We consider the pandemic challenges introduced for each of these six functions and offer several actions to consider in response.
Pandemic Challenge
Uncertainty is high in Planning and Forecasting with changes to asset management plans being the key driver. This requires extreme flexibility with options when things change. The keys to success will be identifying options to accelerate or delay work to control costs, revise asset management plans, and account for changes in labor productivity and availability. Close coordination and cooperation between business units, procurement, vendors, and customers will be needed to identify and capture opportunities. |
Actions to Consider
|
|
For Strategic Procurement, responding to cost pressures should start with three key analyses in the strategic sourcing framework—spend, market, and supplier analyses. With updates to each of these three, refreshed sourcing strategies to meet the current challenges of the pandemic and new assumptions in the “next normal” will be the primary levers businesses can pull to bring costs in line with revenue.
Risk management is a heightened driver in strategic procurement, and it brings with it a requirement to work collaboratively to review total cost beyond unit pricing. It also emphasizes development of sources geographically closer to the point they will be used. Additionally, risk management will reach upstream to bring to light labor and global supply chain risks in supply chains of suppliers. With new sources of supply, quality assurance and control must be maintained. |
|
|
Pandemic Challenge
A leading practices service delivery model for Operational Procurement has become increasingly vital during the COVID-19 pandemic. Among other benefits, this model enables remote work by allowing the right people to have the right access to the right information and for customers and suppliers to continue working “like before” with supply chain. A leading practices service delivery model also facilitates access to supply chain services for vendors and internal customers through a portal and service center supported by a knowledgebase while providing better allocation of work to resources. Even in a WFH environment, transactional work can proceed “almost as normal,” complex issues can be escalated to specialists, and emerging strategic opportunities can be identified and routed to strategic procurement. |
Actions to Consider
|
|
For Logistics, changes in business needs and priorities are placing a premium on flexibility. At the same time, social distancing is making some logistics operations more difficult, risky, and time-consuming.
New requirements for getting the work done will impact collective agreements and require collaboration to address. Third-party logistics providers will be worthy of re-examination as competitive positioning changes due to social distancing and quarantine restrictions. |
|
|
Pandemic Challenge
In Materials Management, the movement of materials is further complicated by new restrictions and changes in priorities. Warehousing and distribution staff will require training to comply with new social distancing and quarantine restrictions, and cross-training will be more important to mitigate the risk to operations of unavailable staff. In general, social distancing is making some operations more difficult and time-consuming. Meanwhile, inventory—the purpose of which is to more efficiently and reliably meet needs in the network—is exceeding or underperforming desired service levels as fundamentals like demand and delivery times change. |
Actions to Consider
|
|
For Accounts Payable, companies who have concerns about working capital are holding on to cash. Some companies are paying certain suppliers sooner to provide additional support where needed. AP is a highly transactional operation, and providing direct access to information through portals and technology to enable self-service can help resolve discrepancies sooner. The pandemic has also re-emphasized the need to have paperless processing to enable teams while they work remotely.
Suppliers are also coping with WFH requirements. This can create more questions, lengthen response times, and complicate dispute resolution. Emphasizing the use of richer communication channels (e.g., video chats) for internal team meetings and supplier sessions can improve the effectiveness of AP. |
|
ScottMadden is actively supporting many clients as they respond to drivers of change and update their supply chain strategies for the “next normal.”
![]() |
Increasing cost pressures
The CFO of a company with $6 billion in annual sales was confronted with an earnings challenge due to revenue declines associated with COVID-19. This executive asked operational leaders in the business to work with supply chain to find strategic cost-reduction opportunities that could help preserve earnings guidance. ScottMadden helped develop plans to capture more than $150 million in savings. |
|
![]() |
Changing plans for asset management
The CEO of a national power and water utility made significant changes in maintenance plans due to the economic and labor impacts of the pandemic. This executive asked operations and maintenance to collaborate with supply chain on their plans. ScottMadden helped integrate the organizations to ensure materials were available to address emergent and scheduled work. |
|
![]() |
Tightening labor constraints
The chief supply officer at a $7 billion company implemented a tiered service delivery model shortly before COVID-19 with help from ScottMadden. The pandemic created increases in demand, supply disruptions, and an influx of business inquiries with shifts in job requirements. Because of the new service delivery model, this client responded faster and with greater effectiveness, even while working from home, than was previously possible. |
|
![]() |
Greater risk from the global supply chain
Multiple leaders sit on supply chain governance councils, which have varying mandates, from sharing vendor information to advising the governments on critical infrastructure that should be covered under the Defense Production Act or stockpiled to lessen the effect of future pandemics. ScottMadden supports these clients in identifying, understanding, and mitigating risks. |
The global response to COVID-19 has resulted in increased cost pressures, changed plans for asset management, tightened labor constraints, and greater risk from the global supply chain. As this article outlines, companies can begin the process of updating supply chain strategies by considering the impacts to each function. ScottMadden can help by assessing your organization against leading practices and emerging strategies to unlock value, ensuring you are prepared to mitigate risks and take full advantage of new opportunities in the “next normal.”
ScottMadden is the management consulting firm that does what it takes to get it done right. We consult in two main areas—Energy and Corporate & Shared Services. We deliver a broad array of consulting services ranging from strategic planning through implementation across many industries, business units, and functions. To learn more, visit www.scottmadden.com | Twitter | Facebook | LinkedIn.
ScottMadden has been a pioneer in corporate and shared services since the practice began decades ago. Our corporate & shared services practice has completed more than 1,900 projects since the early 90s, including hundreds of large, multi-year implementations. Our clients range across a variety of industries from energy to healthcare to higher education to retail. Examples of our projects include business case development, shared services design, and shared services build support and implementation.
We know energy from the ground up. Since 1983, we have served as energy consultants for hundreds of utilities, large and small, including all of the top 20. We focus on Transmission & Distribution, the Grid Edge, Generation, Energy Markets, Rates & Regulation, Enterprise Sustainability, and Corporate Services. Our broad, deep utility expertise is not theoretical—it is experience based. We have helped our clients develop and implement strategies, improve critical operations, reorganize departments and entire companies, and implement myriad initiatives.
John Francis is a partner and co-leads the firm’s supply chain community of practice, Marc Miller is a partner, and Jason Payton is a director.
View MoreSussex Economic Advisors is now part of ScottMadden. We invite you to learn more about our expanded firm. Please use the Contact Us form to request additional information.